Combat Corrosion Before It Happens
Welcome to our blog post on corrosion prevention and control methods for manufacturers in Cleveland, Ohio, and beyond. With over 40 years of experience in metal finishing, we understand the importance of ensuring product durability in various industries, including automotive, military, medical, and more. In this article, we will explore practical strategies to combat corrosion and protect your products from the damaging effects of oxidation and rust. By implementing these methods, you can enhance your manufactured goods’ lifespan, reliability, and performance.
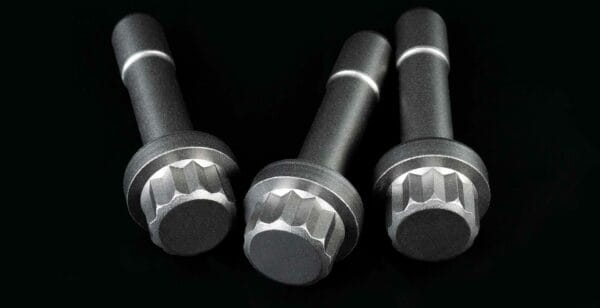
Understanding Corrosion:
Before diving into the prevention and control methods, let’s first understand what corrosion is and how it occurs. Corrosion is a natural process where metals deteriorate due to chemical or electrochemical reactions with their environment. Factors such as moisture, oxygen, temperature variations, and contaminants contribute to corrosion.
To combat corrosion effectively, it is crucial to identify the specific type of corrosion affecting your products. Common forms of corrosion include general corrosion, localized corrosion (pitting and crevice corrosion), galvanic corrosion, and stress corrosion cracking. Once you understand the corrosion mechanism, you can choose the most suitable preventive measures to protect your products.
Corrosion Prevention Methods:
- Surface Coatings: Applying protective surface coatings is an effective method to prevent corrosion. Options include paints, powder coatings, and electroplating. These coatings act as a barrier t between the metal and the environment, shielding it from moisture, chemicals, and other corrosive agents. Choose coatings specifically designed for corrosion resistance, and consider factors such as adhesion, thickness, and compatibility with the substrate material.
- Cathodic Protection: Cathodic protection involves making the metal to be protected by the cathode of an electrochemical cell. This process, commonly achieved through sacrificial anodes or impressed current systems, directs the corrosive reactions away from the metal surface. Sacrificial anodes, usually made of zinc or aluminum, corrode sacrificially, protecting the metal they are attached to. Impressed current systems use a power source to generate a protective electrical current. Cathodic protection is especially useful for structures exposed to water or soil.
- Alloy Selection: Choosing the right alloy for your manufacturing processes can significantly improve corrosion resistance. Stainless steels, aluminum alloys, and certain nickel-based alloys are renowned for their corrosion resistance. Understand the environmental conditions your product will face and select alloys with properties that withstand those conditions. Additionally, consider factors like temperature, pH levels, and exposure to chemicals or abrasives.
- Proper Design: Incorporating good design practices can help minimize corrosion risks. Consider factors such as drainage to prevent stagnant water accumulation, avoiding crevices and sharp corners that trap moisture, and ensuring proper ventilation to minimize humidity levels. Smooth surface finishes also discourage the accumulation of corrosive substances and make cleaning easier. As far as coating performance.. manufacturers should pay more attention to radiuses and surface texture. The smaller or sharper the edge, the more likely your topcoat will wear through, chip, or nick very easily, leaving the base substrate exposed to the elements. An abrasive finish that gives the topcoat a way to anchor itself can also add years to a component’s service span.The primary reasons are under-engineering for cost savings and purposely not wanting a component to endure time, thus more future sales and creating a competitive edge with lower prices. Another major factor is Incoming raw material. Purchasing metal stock guarded against moisture and other chemicals can be challenging, especially today when supply chains are diminishing, and manufacturers are forced to take what they can get. Remember!! Material stock coming into your facility that has already suffered from corrosion is likely to have some residual corrosion buried deep within, even after abrasive blasting, chemical treatments, or machining. Think of metal oxidation as cancer in metal. It’s difficult to get rid of.
- Maintenance and Inspection: Regular maintenance and inspection are crucial to identify and address potential corrosion issues early on. Establish a maintenance schedule that includes cleaning, surface inspections, and reapplication of protective coatings when necessary. This proactive approach can significantly extend the lifespan of your products and prevent expensive repairs or replacements. Halo Metal Prep, Inc specializes In cleaning and removing localized corrosion, leaving still valuable components ready for re-coating and allowing them to be put back Into service.
- Environmental Controls: Controlling the environment surrounding your products can play a vital role in corrosion prevention. Maintain proper humidity levels, control temperature fluctuations, and minimize exposure to corrosive gases or chemicals. Implementing protective measures, such as using desiccants, VCI products, water-soluble/petroleum-based RP’s, or dehumidifiers in staging/storage areas, can help mitigate corrosion risks.
Combatting Corrosion Conclusion:
In the manufacturing industry, combating corrosion is essential for ensuring product durability and reliability. By implementing the strategies mentioned above – including surface coatings, cathodic protection, proper alloy selection, good design practices, regular maintenance and inspection, and environmental controls – you can significantly enhance the corrosion resistance of your manufactured goods.
Remember, preventing and controlling corrosion is an ongoing process that requires diligence and proactive measures. By incorporating these methods into your manufacturing processes, you can minimize the detrimental effects of corrosion and ensure the longevity and performance of your products.
At Halo Metal Prep, Inc., we specialize in providing comprehensive metal finishing services tailored to meet your specific corrosion prevention needs. With our expertise and state-of-the-art facilities, we can help you optimize the durability and reliability of your products.
Contact us today to learn more about our corrosion prevention and control solutions. Together, let’s protect your manufactured goods from the damaging effects of corrosion and elevate your product quality to new heights.