Metal finishing is a process that involves improving the appearance, durability, and functionality of metal products. One of the most effective methods of achieving this is media blasting, also known as abrasive blasting. Media blasting involves propelling abrasive particles at high speeds onto the surface of metal objects to remove surface contaminants, smooth rough surfaces, and prepare surfaces for further processing.
Media Blasting
Several types of media blasting materials are available, each with unique properties that make it suitable for specific applications. This article will explore the different types of media blasting materials and the best applications for each.
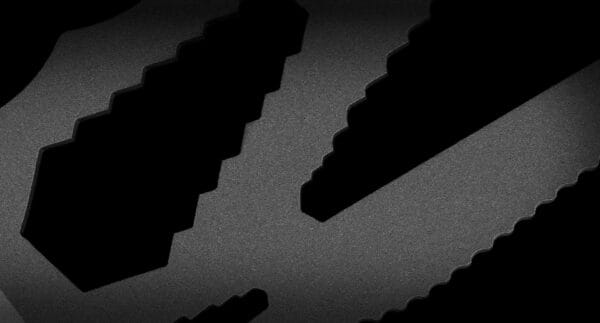
Sand
Sandblasting is the term most commonly used type of media blasting, and it involves propelling sand particles onto metal surfaces at high speeds. Sandblasting effectively removes rust, paint, and other contaminants from metal surfaces. Sandblasting is also effective in smoothing rough surfaces and preparing metal surfaces for further processing.
Sandblasting is ideal for heavy-duty applications such as removing rust and paint from large metal structures, cleaning industrial equipment, and preparing surfaces for welding. However, the use of sand in sandblasting has been phased out in many parts of the world due to concerns about health and environmental hazards.
One of the main reasons why sand is no longer used in sandblasting is because of the health risks associated with inhaling the fine particles of silica that are produced during the blasting process. Prolonged exposure to silica dust can lead to a variety of respiratory problems, including silicosis, which is a serious and incurable lung disease.
In addition to health concerns, the use of sand in sandblasting also creates environmental hazards. The dust created by sandblasting with sand can contaminate the air, soil, and water in the surrounding area. This can have negative impacts on both human and animal health, as well as the natural ecosystem.
As a result, many governments and industries have moved away from using sand as an abrasive material in sandblasting. Instead, alternative materials such as garnet, aluminum oxide, or glass beads are now commonly used. These materials are safer for workers and have less of an impact on the environment.
Overall, the shift away from sandblasting with sand is a positive development for both human health and the environment. While sand may have been an effective abrasive material in the past, it is now widely recognized as a hazardous and unsustainable choice.
Glass Beads/Peening
Glass bead blasting involves propelling tiny glass beads at high speeds onto metal surfaces. Glass bead blasting is effective in removing surface contaminants, rust, and scale from metal surfaces while producing a smooth bright satin finish. Glass bead blasting is also ideal for cleaning and honing delicate surfaces, such as aluminum and other non-ferrous metals, without causing any damage.
Glass bead blasting is ideal for applications that require a clean, polished finish, such as aerospace components, medical equipment, and automotive parts.
Aluminum Oxide
Aluminum oxide blasting involves propelling aluminum oxide particles at high speeds onto metal surfaces. Aluminum oxide blasting is effective in removing surface contaminants, rust, and scale from metal surfaces. It is also effective in creating a matte finish on metal surfaces, making it ideal for applications that require a textured finish.
Aluminum oxide blasting is ideal for preparing metal surfaces for painting, powder coating, preparation for bonding, and other finishing processes. It is also suitable for cleaning and preparing metal surfaces for welding.
Steel Grit
Steel grit blasting involves propelling tiny angular steel particles at high speeds onto metal surfaces. Steel grit blasting effectively removes rust, scale, and other contaminants from metal surfaces. It also effectively creates a textured finish on metal surfaces, making it ideal for applications that require a rough surface or anchor pattern.
Steel grit blasting is ideal for heavy-duty applications such as preparing metal surfaces for painting, powder coating, deflashing, and other finishing processes. It is also suitable for removing weld spatter and other surface imperfections from metal components.
Steel Shot
Steel shot blasting involves propelling small steel balls at high speeds onto metal surfaces. Steel shot blasting is effective in removing rust, scale, and other contaminants from metal surfaces while also creating a textured or peened finish. This process is suitable for removing surface imperfections from metal components, such as burrs and sharp edges.
Steel shot blasting is ideal for heavy-duty applications such as cleaning and preparing large metal surfaces, removing paint and coatings, and preparing surfaces for painting, powder coating, or plating.
Ceramic Peening
Ceramic peening is a specialized type of media blasting that involves propelling small ceramic beads at high speeds onto metal surfaces. Ceramic peening creates a compressive stress layer on the surface of the metal, which improves its resistance to fatigue and stress corrosion cracking.
Ceramic peening is an excellent alternative to glass bead blasting when consistency and media degrading are of concern. Glass beads are known to degrade over time, which can lead to inconsistencies in the blasting process and result in variations in the surface finish. Ceramic peening, on the other hand, uses ceramic beads that are much more durable and resistant to degradation.
Ceramic peening is an ideal option for applications that require a consistent surface finish, such as aerospace and automotive components. The process is suitable for treating a range of materials, including steel, titanium, aluminum, and composites.
In conclusion, media blasting is an effective metal finishing process that propels abrasive particles onto metal surfaces at high speeds. Several media blasting materials are available, each with unique properties that make it suitable for specific applications. By selecting the best media blasting material for a specific application, you can ensure that your metal products will look great and perform well for many years to come.